Monitoring of Shinkansen RC Viaducts
Background
The Shinkansen (Bullet Train) railway viaducts, built over 40 years
ago, are aging and are continuously subjected to increasing service
loads and severe earthquakes. The number of Reinforced Concrete (RC)
viaducts in service between Tokyo and Osaka alone is over 1000
blocks. This does not include the viaducts that connect other major
cities going north and south of Japan. Thus, there is a need for
retrofitting and repair, coupled with continuous monitoring of
existing viaducts in order to ensure safety and reliability of
transportation.
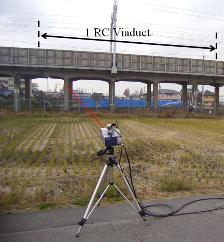 |
Fig.1 Scanning LDV |
Measurement Systems
In the Bridge and Structure Laboratory, we are developing safe, smart
and fast monitoring systems that use high-technology sensors and
equipment. We are using laser Doppler vibrometers or LDV (single-point
and scanning types), servo-accelerometers, servo-velocimeters,
wireless tri-axial accelerometers and piezo-accelerometers for
measuring ambient, train-induced and impact vibrations. The data
collected are then processed using system identification techniques to
determine the dynamic properties of the viaduct and check if there are
any changes that may indicate damage.
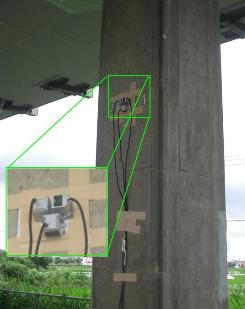 |
Fig.2 Servo-accelerometers for 3D Measurement |
Finite Element Model
We are also using finite element modeling to derive models of the RC
viaduct. This is an important step because we are dealing with a real
structure that cannot be damaged for study. But using the FEM model we
can simulate damage at critical locations of interest and determine
how the dynamic properties of the viaduct change with increasing
damage. Figure 3 shows the global lateral mode shape of a finite
element model of a viaduct.
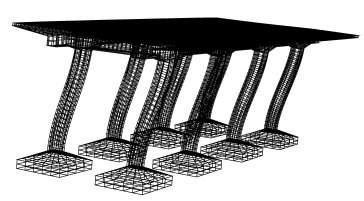 |
Fig.3 Lateral Mode of an RC Viaduct |
|